Let’s Bring Your Vision to Life
Designing and manufacturing flexible protective solutions for upstream and downstream powder processing in your facility, lab, or plant. Explore your single source for bioprocessing.
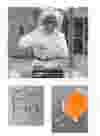
Premier Bioprocessing Workstream Experts
ILC Dover is a world leader in innovative design and production for biopharmaceutical, pharmaceutical, medical device, and aerospace markets. For over 25 years, we’ve led the industry in single-use powder and liquid handling, solving life sciences’ most complex bioprocessing challenges. We uphold our mission to deliver custom containment solutions so you can uphold your mission to deliver life-saving therapies.
ILC Dover is a global supplier of flexible, single-use systems and aseptic solutions that support upstream and downstream biopharma manufacturing processes.
ILC Dover is a global supplier of flexible, modular, single-use pharmaceutical manufacturing solutions for sterile and aseptic pharma processing.
ILC Dover’s personal protective equipment mitigates the risks of exposure to airborne pathogens, infectious diseases, and active pharmaceutical ingredients.
Discover our bulk packaging solutions for liquid and dry products, ranging from bulk liquid and bulk dry liners to paper and rigid IBCs.
Designing and manufacturing flexible protective solutions for upstream and downstream powder processing in your facility, lab, or plant. Explore your single source for bioprocessing.
We provide world-class process engineering with end-to-end support for your projects, including custom drawing turnaround in just five days. Whether you’re a small startup or a large corporation, our adaptable solutions are tailored to meet your unique challenges and goals. With engineers spanning three continents, we stand ready to assist you from concept to production and validation.
Our solutions are distinguished by superior consistency and conformance, driven by an efficient business management system that oversees operations for consistency and excellence. Each component undergoes construction and inspection in ISO-certified facilities, employing validated methods to meet rigorous quality standards prior to delivery to your facility.
One of the world’s largest pharmaceutical companies needed to streamline powder handling processes for enhanced drug production. ILC Dover provided a comprehensive, custom solution: the EZ BioPac® system as well as a stainless-steel lifting mechanism and drum dolly.
The weigh and dispense team at a global CDMO specializing in pharmaceutical development and manufacturing services for protein-based biologics as well as cell and gene therapies approached ILC Dover for a better way to fill 5L, 10L, and 15L 2D powder bags.
ILC Dover Unveils Sentinel XT™ Horizon for Innovative Respiratory Protection with Unmatched Comfort & Safety
ILC Dover's SCape CO/CBRN 30 Escape Respirator Receives CE and UKCA Certification, Setting New Standard for Respiratory Protection
Ingersoll Rand Names Scott Watson as Leader for Life Science Technologies Platform
ILC Dover is hiring as we continue to meet increased demand within the life sciences and aerospace industries. Join our team to go beyond boundaries.